My workshop does not allow me to spray so I need to wait for ambient temperatures above 16°C (65°F) to start priming outside. As this is expected not before April/May I went on preparting parts – rudder next.
Priming
Digging into the staff of priming and especially the aerospace specific zinc-hexochromate substances I decided against using such hazardous products. I neither have a suitable place to use it safely nor do I consider the semi-professional use of such substances being safe for my envirmonment and personal health.
Although not required and mandated by VANS and even my supervisor advised against – I decided to prime all parts using EKOPrime from Steward Systems and place the order for „smoke grey“ EKOPrime, EkoClean and EkoEtch with LAS aerospace. Main reason for doing so is, that during preparation of all the parts scratches of the ALCLAD pure aluminium layer are difficult to avoid – apllying a thin layer of primer will seal and also will more scratch resistant thereafter (the ALCLAD layer can be scratched easly by nail).
Construction starts with separting parts using the bandsaw. A little care is needed to stay on the cut line. I preferred to remove the downside vynl after separation and smoothing the cutlines with the file.
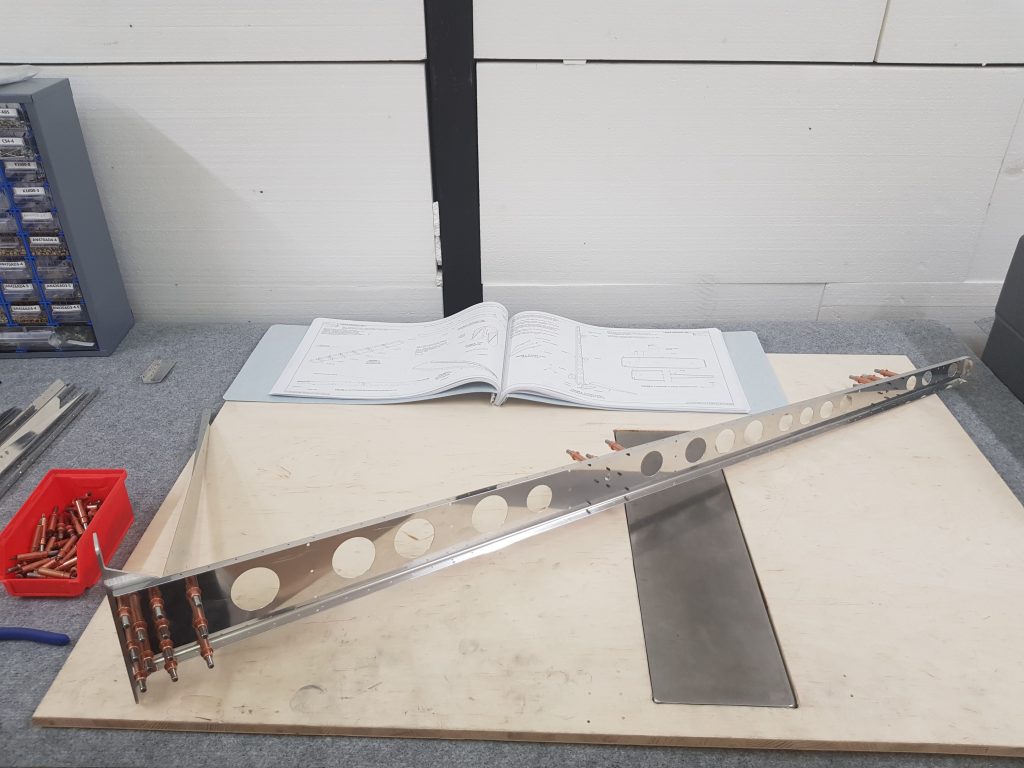
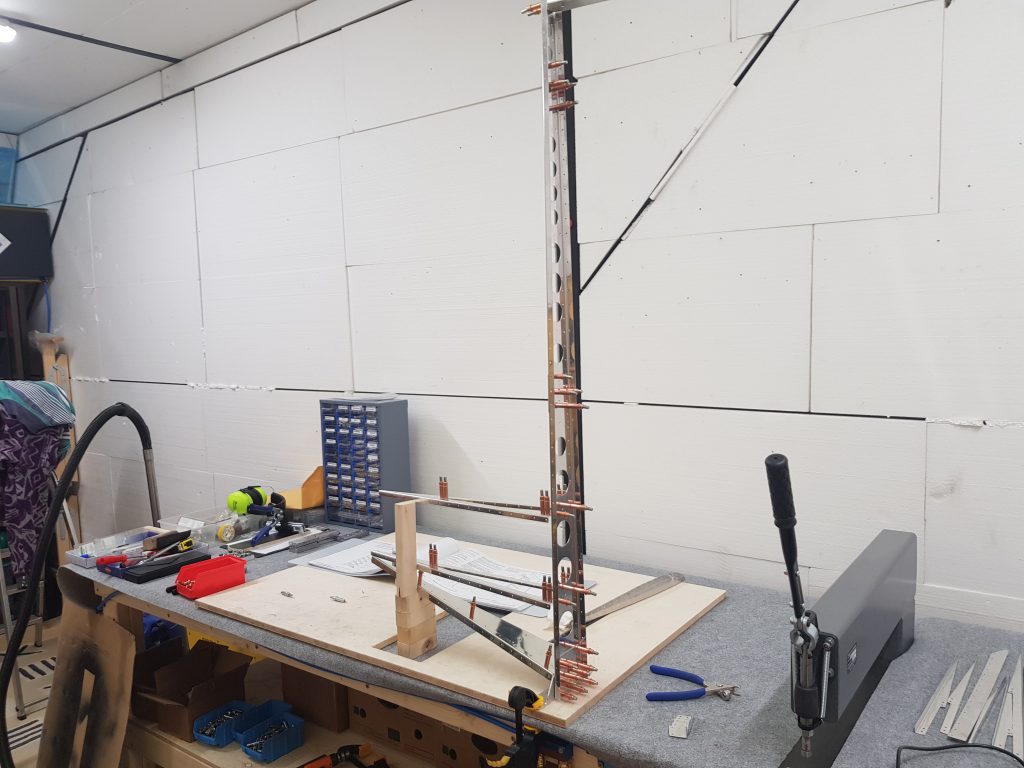
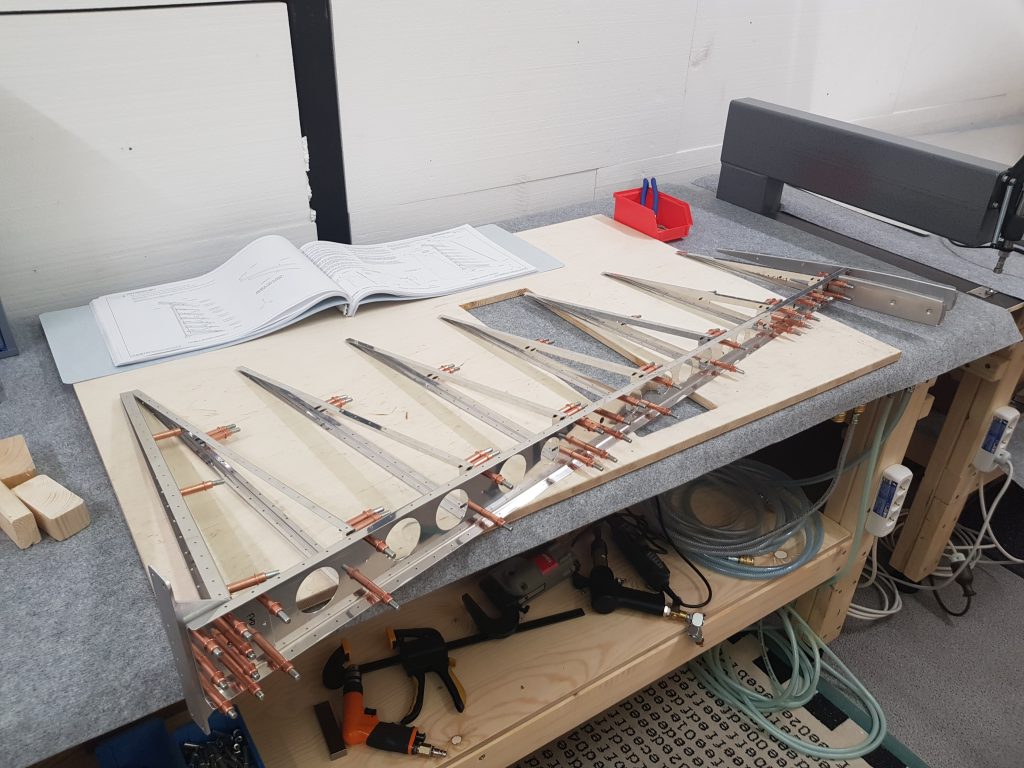
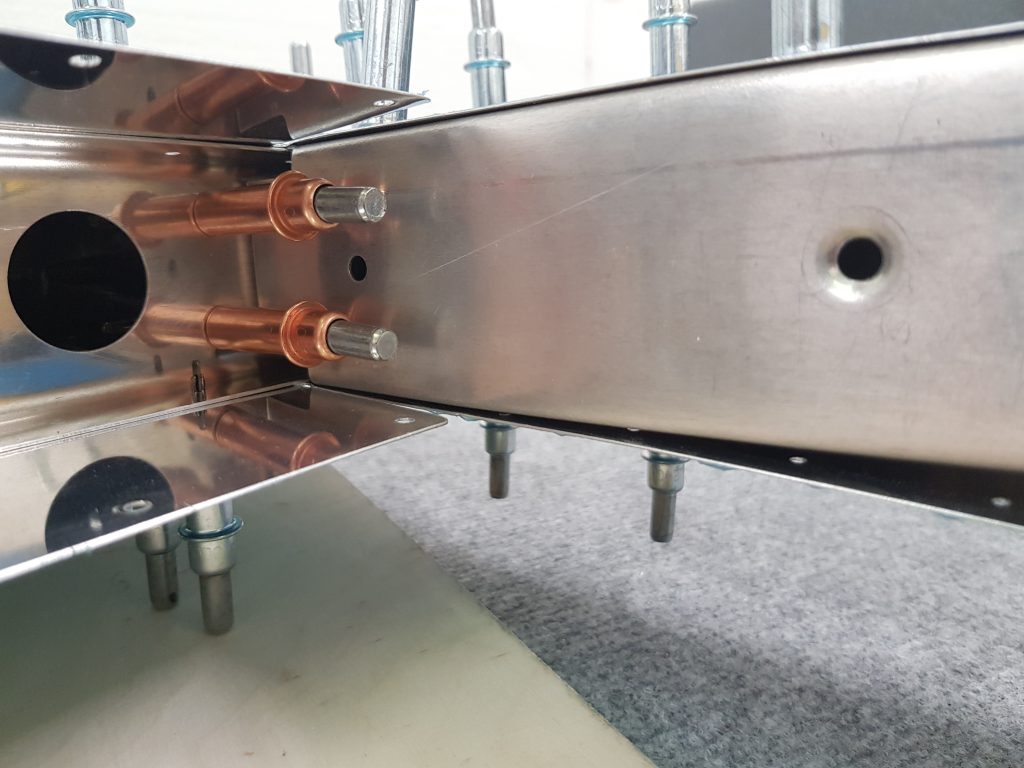
The most difficult part was fluting the R-903 und R-912 top rips to become straight and allow the skins to align properly with prepunched rivet holes.
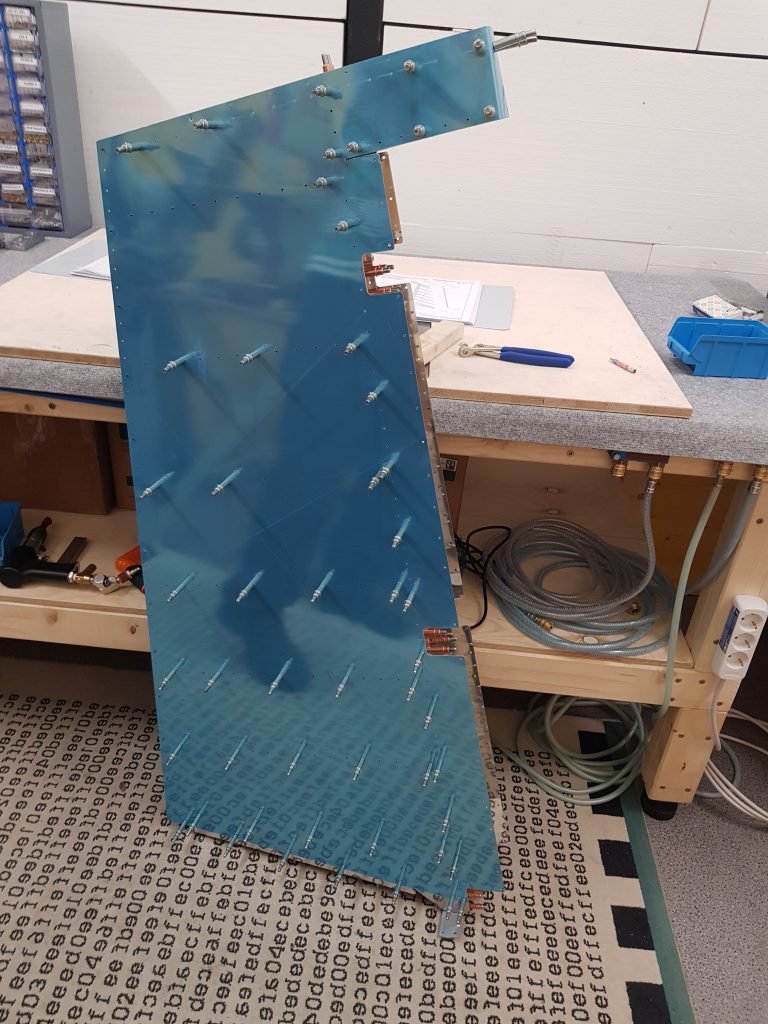
Match drilling the trailing edge I followed the methods of several VAN’s builders using a L-profile aluminium (40x40x3mm) which is match drilled with the trailing edge, step by step progressing from middle to both ends symmetrically. For riveting every 5th hole if the aluminium angle is enlarged to 13mm to accept a normal size squeezer’s die for flush rivets.